CASE STUDIES
Performance Management System
Client Industry: Manufacturing - Medical and Pharmaceuticals
The idea is straightforward: Without measurement, effective management is impossible. The DMT Methodology has empowered our client to establish a SMART FACTORY, which has been instrumental in developing and honing Key Performance Indicators (KPIs) that align with their strategic vision. These KPIs span across vital areas such as production line efficiency, equipment uptime, quality control, material yield, and warehouse utilization. With these metrics, executives and stakeholders are now equipped with the visibility needed to monitor and improve their team’s performance through the implementation of a short-interval control system and regular team huddles at various organizational levels.
Change management and digital transformation ensure the sustainability of both financial and operational improvements. AI-enhanced tools such as, OEE Alert, Machine Vision Inspection, and ML-powered forecasting, further tackled pressing business challenges.
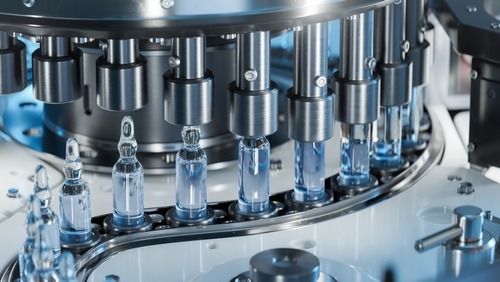
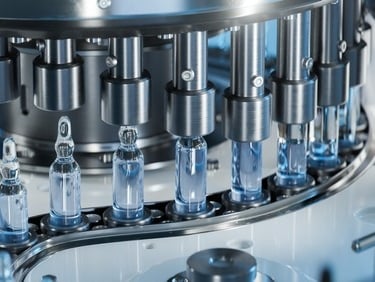
Transformation:
Direct Labor Savings by significant reduction in changeover times and equipment downtime. This, coupled with enhanced training programs has improved labor productivity by 25%.
Material Cost Savings realized through a 10% reduction in material waste, thanks to optimized material usage and process improvements.
Quality Rework Reduction by implementing a formal training program and improving quality control measures, resulting in a 40% decrease in rework costs.
Changeover Time Reduction by streamlining the changeover process, the facility improved line availability by 5%, allowing for more efficient production runs and less idle time.
Late Orders Reduction enhanced the logistics flow and also led to a 35% reduction in late order fees, and boosting customer satisfaction. Most importantly, the elimination of backorders has allowed the production floor and office staff to work stress-free.
Digital Transformation & Change Management ensure sustained results and foster a culture of ongoing improvement.
Diagnostics:
Before the project’s implementation, the facility operated without established metrics to evaluate the performance of its eleven manufacturing lines and the distribution center. These lines suffered from low efficiency, largely due to frequent and prolonged changeovers, as well as significant equipment downtime. Such inefficiencies led to consistent order delays and a congested warehouse, disrupting the flow of logistics.
A notable lack of a formal training program for the operational staff contributed heavily to an increase in quality complaints, damaging the company’s reputation and inflating the cost of rework.
Additionally, the operations and finance teams encountered substantial challenges in creating a realistic budget due to the significant overuse of labor and materials with no clear justification specially on the material side. Furthermore, there was a clear absence of a continuous improvement mindset on the factory floor, a critical component for achieving operational excellence.
Modifications:
DMT has successfully implemented a performance management system that adheres to the principles of a smart factory. This advanced system provides immediate insights into production metrics and identifies the root causes of any performance issues at both the production line and SKU levels. The production lines are outfitted with either digital or manual communication boards that display the quantity produced versus the target, along with a concise explanation of the main reason codes that disrupted the expected production. DMT has developed Key Performance Indicators (KPIs) that are in harmony with our clients’ strategic objectives. Our ‘Visual Factory’ approach enables interdisciplinary teams to proactively tackle critical issues concerning quality, materials, equipment, and planning. Client's workforce participates in Short Interval Control (SIC) sessions every four hours, closely examining production data and the factors contributing to less-than-optimal performance. Following this, teams engage in intelligent problem-solving workshops, where they formulate digital action plans that specify both temporary and long-term solutions, complete with assigned timelines and responsible parties.
The client has eradicated primary equipment downtime causes and lengthy changeovers across seven production lines. Interventions like predictive and preventative maintenance, along with SMED, enhanced plant uptime. The client also resolved material loss causes in all production lines, attributed to waste during changeovers and production due to equipment malfunctions or incorrect setups for certain products. A new smart tracking system was introduced to oversee order lead-times and due dates, alerting product managers to expedite production and shipping with minimal delay when due dates were missed. This measure significantly cut the shipping costs.
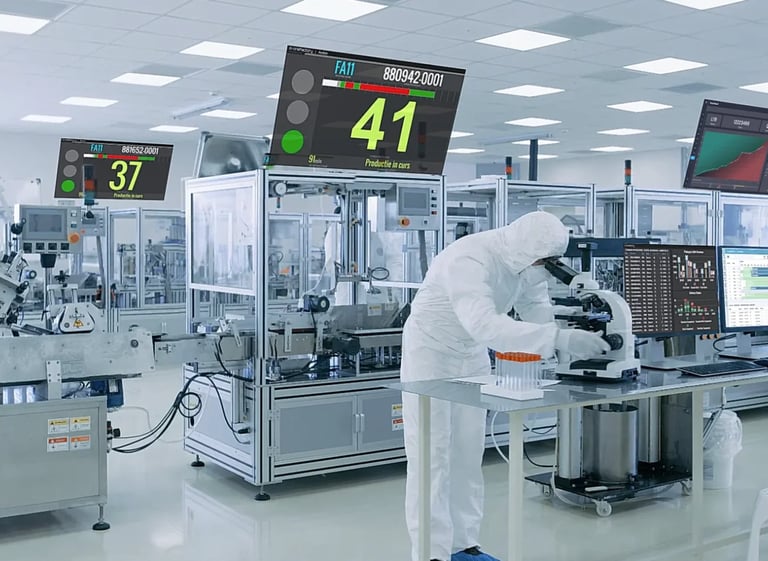
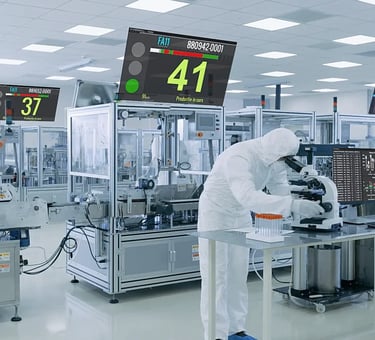
Agile Manufacturing
Client Industry: Manufacturing - Medical Devices & Pharmaceutical Supplies
The DMT's agile manufacturing approach markedly enhanced the client’s production systems. Streamlining material handling and inventory processes improved material flow, enabling efficient changeovers and small-order fulfillment. Despite managing over 10,000 components for 1,500+ SKUs on 14 lines, the new system reduced changeover impact on line efficiency, delivery timeliness, and raw materials storage requirement. Moreover, it improved inventory accuracy and minimized shipping penalties. The project notably cut lead times for high-volume products from 2-3 weeks to just 5 days, substantially lowering working capital and finished goods storage expense.
Change management and digital transformation ensure the sustainability of both financial and operational improvements. AI-enhanced tools such as ML-powered forecasting and Predictive Changeovers Optimization further tackled pressing business challenges.
Transformation:
Direct Labor Efficiency: Reduced labor costs by 20% through streamlined order-picking and SMED for changeovers.
Storage Optimization: Decreased storage space by 15%, leading to a significant cost reduction.
Inventory Accuracy: Improved inventory tracking reduced discrepancies by 30%, significant saving in potential shipping penalties annually.
On-Time Delivery: Enhanced scheduling accuracy increased on-time delivery by 10% while decreed the lead-time from 2-3 weeks to 5 days.
Customer Satisfaction: 4% improvement in the related corporate metrics that is tied to the organizational objective
Changeover Downtime: Minimized changeover times resulted in a 15% productivity boost and also reduced the indirect headcount by 10% for the staging purposes.
Digital Transformation & Change Management ensure sustained results and foster a culture of ongoing improvement.
Diagnostics:
The order-picking and warehouse management system faced significant challenges, resulting in inventory discrepancies and transactional confusion. These issues led to extended changeover times, increased labor costs, material shortages, and expensive reworks. The root cause was incorrect components being picked for assembly work orders.
Moreover, the client suffered hefty penalties due to late shipments, and its market competitiveness declined significantly. The inability to produce small batches with the right product mix tailored to customer needs, exacerbated the situation. To cope, the client resorted to external storage for finished goods, allowing them to handle fluctuations in customer demand at a higher cost.
Modifications:
The agile manufacturing system has significantly improved the client’s ability to respond rapidly to customer demands, leveraging speed and agility as a key competitive advantage. The introduction of a new order-picking system, seamlessly integrated with the existing ERP, has streamlined the production team’s preparation process for components required in finished good work orders.
"Wave Picking" and "SMED" are at the core of this system; component stagers select shared components from multiple orders and organize them into individual orders within a newly established staging area. Consequently, the client can now execute scheduled work orders punctually and error-free, while minimizing downtime during changeovers.
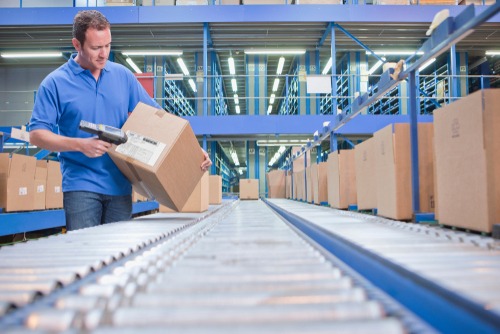
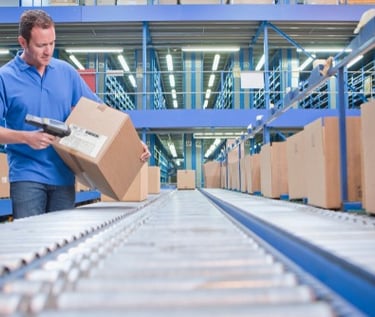
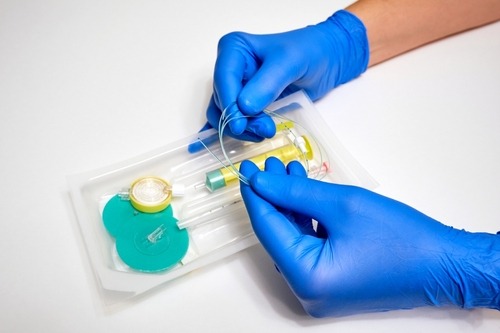
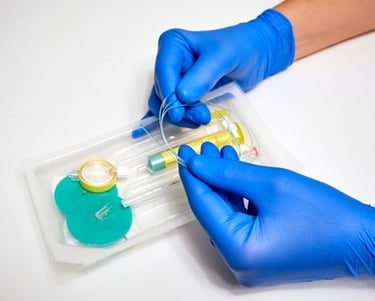
Material Yield Improvement
Client Industry: Manufacturing - Food & Bakery
The DMT Methodology was instrumental in assisting the client to pinpoint and address the underlying issues contributing to an additional 10% in material losses. The primary focus was on diagnosing raw material losses during changeovers, as well as reducing finished goods wastage throughout the material handling process. Furthermore, the executive team previously lacked the necessary data to determine the appropriate material yield factor for accurate costing and pricing. Following the implementation of changes, DMT facilitated the creation of a dynamic material consumption estimator, which updates standards annually at the SKU level.
Change management and digital transformation ensure the sustainability of both financial and operational improvements. AI-enhanced tools such as ML-powered material waste reduction and Intelligent Material Weight Checkers saved significant material values across manufacturing processes.
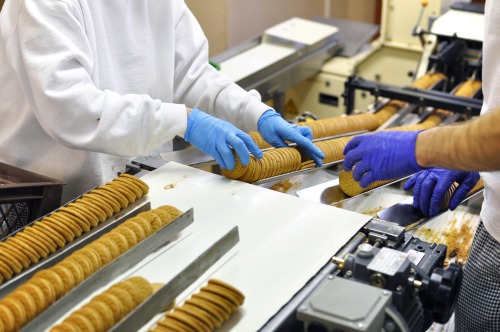
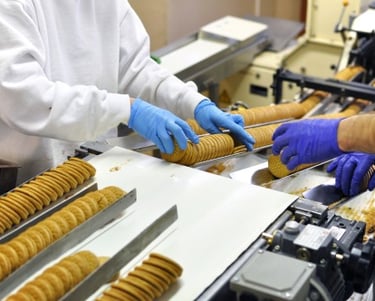
Transformation:
Material Cost Savings: Achieved a 9% reduction in material costs by minimizing waste and excess use of ingredients.
Inventory Accuracy: Enhanced precision in inventory due to the alignment of production component quantities with the Bill of Materials (BOM) standards.
Operational Efficiency: Significant improvements in material handling and production scheduling have increased overall operational efficiency by 4%.
Continuous Improvement Culture: The client has developed the ability to independently refine and advance their inventory strategies.
Automation and AI: Introduction of an innovative and smart system for precise monitoring of material utilization and estimation of raw material consumption at the SKU level for all recipes.
Competitive Advantage: Marketing team can now offer more cost-effective products, outperforming competitors without compromising on quality.
Digital Transformation & Change Management ensure sustained material usage and foster a culture of ongoing improvement.
Diagnostics:
The customer faced two primary challenges: excessive material usage and a discrepancy between financial reports and the physical inventory in the warehouse.
This inconsistency in inventory posed a significant issue for the Material Requirements Planning (MRP) system, resulting in excessive usage of ingredients and an increase in labor costs. The latter was due to downtime associated with material shortages and the need for repeated machine setups due to schedule changes in work orders. To mitigate these issues, the client opted to increase the safety stock levels for essential components, albeit at a considerably higher expense
Modifications:
During the project’s initial six months, DMT implemented decisive corrective measures. These included adjusting equipment recipes to align with the standard quantities listed in the Bill of Materials (BOM) and calibrating the load cells in the filling machines. Subsequently, our Continuous Improvement (CI) team concentrated on identifying the root causes of the inefficient scheduling process and the expensive reworks. As a result, we observed a reduction in material consumption along with a significant improvement in inventory accuracy. A robust control plan was put in place to maintain the financial results, ensuring equipment fill accuracy and an enhanced material handling process. Furthermore, we introduced an automated and dynamic system to estimate material consumption at the BOM level, which allows for periodic updates to the financial standards

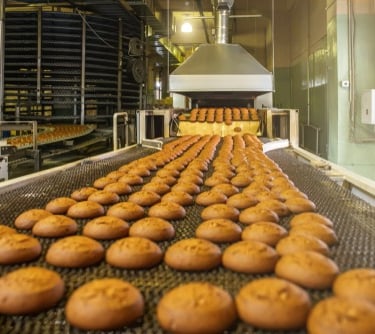
Product Costing Optimization
Client Industry: Instrument Transformers Manufacturer
The DMT Methodology has empowered the client to enhance their financial benchmarks significantly. This includes elevating standards for direct labor costs, material consumption rates, and overhead expenses across all production lines and individual Stock Keeping Units (SKUs). The implementation of an automated data collection system was a pivotal step in this transformation. It facilitated the development of an innovative product costing framework, which systematically compiles and analyzes historical data on actual manufacturing expenses.
This robust framework is subjected to a comprehensive evaluation and refinement process annually, which underscores its adaptability and relevance.
Furthermore, the AI-Powered Product Cost Estimator, provides strategic recommendations for optimizing Finished Goods (FG) inventory management systems.
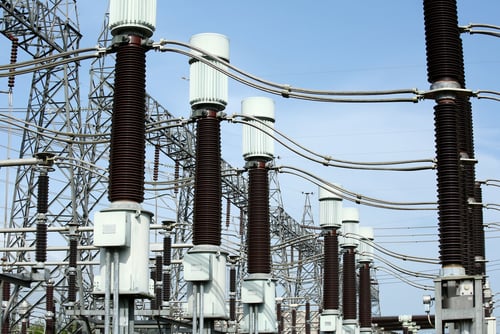
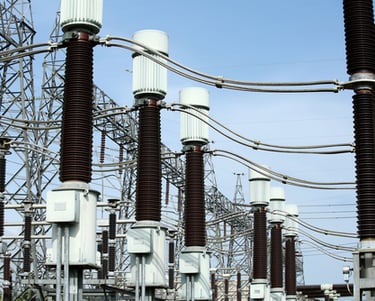
Transformation:
Financial Precision: Enhanced cost calculations for direct labor, material consumption, and overhead, improving financial benchmarks across production lines and SKUs.
Automated Costing Framework: An automated data system now underpins a novel product costing framework, informed by historical cost data and subject to annual refinement.
The SKU rationalization team, leveraging the new system, discontinued 15% of unprofitable SKUs. This move enhanced production efficiency and warehouse space utilization by substituting these products with more profitable SKUs.
Data Collection Overhaul: Reduced reliance on manual data processes, streamlining the review and adjustment of labor and material standards.
Capital Investment Justification: A dynamic data system substantiated business cases for capital investments, modernizing production lines.
Competitive Edge: The S&OP team leverages the smart costing system to refine inventory strategies, offering more cost-effective products and outperforming competitors through improved plant utilization and optimized capacity.
Informed Decision-Making: Stakeholders now make data-driven decisions regarding inventory at the line and SKU levels, thanks to the new system.
Diagnostics:
The existing product costing system fell short in providing the required flexibility and precision at both the production line and SKU levels. Although the standard cost estimates were fairly precise at the plant-wide scale, there was a deficiency of granular data that hindered the refinement of inventory strategies at the SKU level. Additionally, the discrepancy between the standard earned hours and the actual labor utilized on the production floor added complexity for business developers. This made it difficult to accurately determine SKU efficiency, establish minimum order quantities, assess material scrap rates, and calculate ideal safety stock levels.
Modifications:
The deployment of innovative direct labor and SKU efficiency reporting systems has facilitated the gathering of precise historical data, which in turn enables accurate financial forecasting at both the production line and SKU levels. The integration of automated data collection mechanisms within the production line has significantly reduced the incidence of human and system errors in performance reporting. Consequently, executives are now equipped with the necessary data to inform SKU strategy decisions, leading to a marked improvement in the factory’s overall operational efficiency.
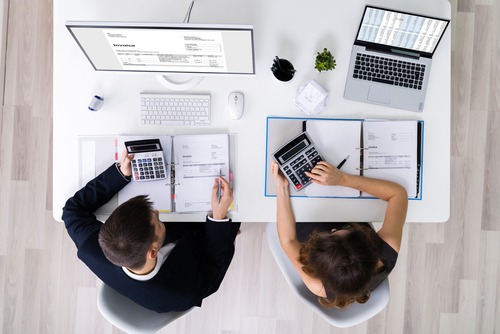
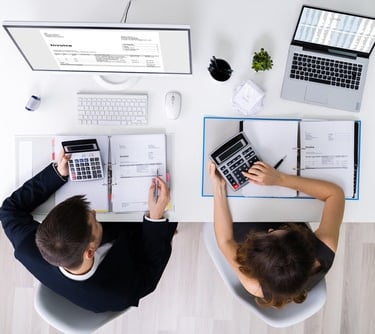
Maintenance & Engineering Revolution
Client Industry: Manufacturing - Chemical Products
The DMT Methodology enabled the client to pinpoint and tackle the main causes of equipment downtime. By adopting a smart maintenance system, plant downtime was halved within nine months. The approach yielded substantial gains by emphasizing total productive maintenance principles. The client now employs a Computerized Maintenance Management System (CMMS), integrated with an automated data collector, for detailed documentation and analysis of downtime reasons. This smart system informs maintenance and engineering leaders in developing strategies to boost plant uptime and reduce maintenance expenses.
Change management and digital transformation ensure the sustainability of both financial and operational improvements. AI-enhanced tools such as ML-powered CMMS and Machine Vision Systems reduced the total equipment downtime significantly.
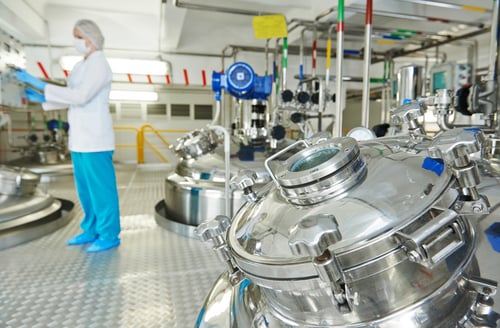
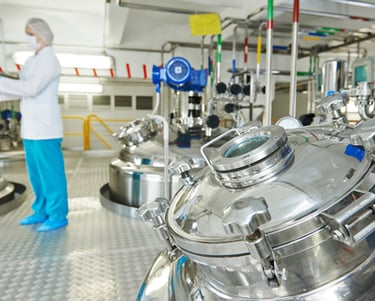
Transformation:
Direct Labor Efficiency: Achieved a 50% reduction in downtime, enhancing productivity. This translates to a proportional decrease in direct labor costs due to less idle time.
MTTR (Mean Time To Repair)Improvement : Improved efficiency in repair times can lead to reduced labor costs for repairs.
MTBF (Mean Time Between Failures): Longer intervals between failures reduce the frequency of repairs, thus saving on labor and parts.
CMMS System Implementation:
The new Computerized Maintenance Management System (CMMS) has improved plant uptime. Preventive and predictive maintenance strategies have likely reduced emergency repair costs and associated overtime labor expenses.
AI and IoT Integration: By leveraging Artificial Intelligence (AI) and the Internet of Things (IoT), the client can anticipate and prevent major machinery failures. This proactive approach can save significant amounts on urgent repairs and unscheduled labor.
Overhead Cost Reduction: Enhancing the reliability of our machinery has enabled the client to significantly diminish overhead expenses. This includes reductions in temporary storage and shipping fees, attributable to more dependable production and shipping schedules. By adopting a strategy closer to the Just-In-Time (JIT) model, rather than a make-to-stock approach, the client has streamlined operations and achieved cost efficiency
Diagnostics:
The plant encountered significant production delays due to unexplained equipment downtime. The absence of a reliable maintenance system worsened the situation, hindering the machinery’s ability to operate consistently within a reasonable maintenance budget. As a result, the costs related to production and maintenance overtime increased, indicating a recurring pattern of equipment malfunctions. It was observed that the downtime was frequently extended due to challenges in sourcing spare parts, exacerbated by an ineffective inventory system. The unavailability of spare parts, along with the extended lead times for their procurement, led to prolonged equipment downtime. This severely disrupted the production schedule, resulting in a substantial negative impact on the on-time delivery metric
Additionally, The client was subjected to considerable additional expenses, such as late delivery penalties, incomplete shipments, and external storage costs. These were primarily due to the unreliability of equipment, which hindered the implementation of an effective Just-In-Time (JIT) inventory system.
Modifications:
The client was able to identify the primary causes of equipment downtime through the new system. These included the lack of preventive maintenance, the unavailability of spare parts, incorrect machine setup, and inadequate installation and commissioning processes for the new machinery. The implementation of initiatives such as 5S, root cause analysis, predictive maintenance, early equipment management, and autonomous maintenance laid the groundwork for the new program.
Additionally, the maintenance team was equipped with an automated data collector (IoT) to log the reasons for downtime, as well as AI tools to analyze the collected data and patterns. These tools also provide recommendations for preventive actions to reduce the risk of equipment failure. Furthermore, the existing Computerized Maintenance Management System (CMMS) was repurposed to schedule overhauls and ensure the timely maintenance of critical spare parts.
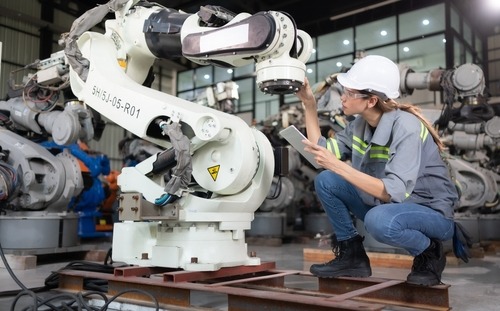
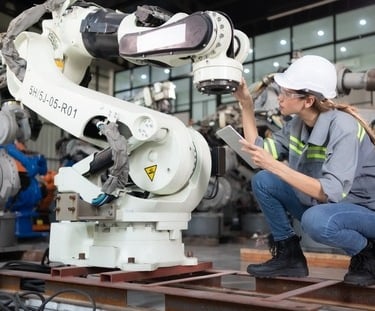
info@efficiency-catalyst.com
1-289-633-3621
©2023-2025 Efficiency Catalyst Solutions Inc.
www.efficiency-catalyst.com
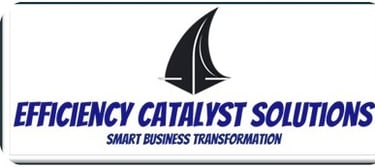
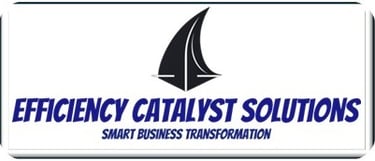